At Setra, safety is a top priority. And the spectacular pendulum impact test with the new Setra MultiClass 500 LE is impressive proof of this. A total of 1.9 tonnes of steel thump the front of the MultiClass 500 LE.
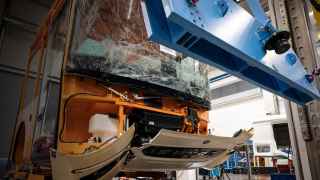
SetraWorld Magazine
It's all for the driver.
Pendulum impact test with the Setra MultiClass 500 LE.
It's all for the driver.
The countdown is on. “Three, two, one”... sounds from the speakers. A long high-pitched warning tone sounds. A giant pendulum with a powerful light-blue steel plate is now released from its horizontal position and strikes the front of the bus with an ear-splitting crash.
The aim of all this racket? Maximum-possible passive safety.
We're in the testing hall for buses/touring coaches and trucks at Daimler Trucks' Development and Testing Centre (EVZ) in Wörth. It's full of impressive testing facilities and a number of chains, shackles, and other items of lashing equipment in various sizes and colours. Here, vehicles, driver’s cabs and torsos are deliberately destroyed... all in the name of the highest-possible level of passive safety.
Safety experts work together.
On site, a group of top safety experts gathered together. This is the team led by Jörg Dünschmann, test engineer and head of the test facility. Peter Schmutz and his colleague Thomas Mönnich from the Daimler Buses testing department, responsible for operational durability and passive safety, are also there. And Oguz Meric, project manager for the development of the bodyshell of the Setra MultiClass 500 LE. Finally, there's Bartholomäus Zak, engineer for type testing and homologation from TÜV Rheinland. He watches the test proceedings like a hawk and will then provide certification – assuming that the results are positive, of course!
The pendulum impact test is not required for buses/touring coaches, but, according to Peter Schmutz, “we ensure that every new model series from Daimler Buses meets the pendulum impact requirements.” After all, safety is part and parcel of the Setra brand. And despite the continuous development of assistance systems, an accident can never be completely ruled out.
Focus on driver protection.
The pendulum impact test is about protecting the driver – in more exact terms, it's about their survival space. “We simulate a rear-end collision with a truck platform”, says Jörg Dünschmann. In such a scenario, the bus driver also needs to be protected. Bartholomäus Zak explains things in more technical terms: "There must be no contact with parts that you cannot push away with a maximum of 100 newtons. These would cause injuries in a real accident."
Precision is essential.
All safety checks in the development centre are carried out strictly in accordance with the applicable standard, which for the pendulum impact test is ECE‑R29.03. This means that absolute precision is a must. The pendulum’s plate weighs exactly 1,913 kilogrammes and is 2.5 metres wide and 80 centimetres high, and was mounted for this test at a height of exactly 4,644 millimetres.
A total of 55 kilojoules is necessary for the pendulum impact test. One joule is the amount of energy you need to lift 100 grammes one metre. So for this test, we're talking about 55,000 times that amount. This means that the plate's weight and the pendulum's height must be calculated down to a tee. The height of the plate impact, the position of the dummy in the centre area – average human height – and all the equipment for the test object must also be precisely specified.
Realistic test conditions.
The test item is the torso of a Setra MultiClass S 515 LE, i.e. a complete skeleton up to and including the front axle with windscreen, panelling on the front end including the headlamps, the major assemblies behind it, such as the air reservoir, and the entrance door. The complete “Basic” cockpit of the new MultiClass 500 is installed inside. Front end, instrument panel, interior trim, steering wheel, driver’s workplace – all these are the same as in the original vehicle.
A detailed setup.
Jörg Dünschmann and his team have carefully braced this torso in place with giant chains and anchored it firmly to the ground. On the driver’s side, a black-and-white patterned adhesive strip – the experts call this piano tape – is used to detect any displacement of the torso that occurs due to the huge impact of the steel plate. Sensors also help with this. Ultra-bright spotlights are directed at the torso, as well as a handful of cameras, including high-speed cameras with up to 2,000 frames per second.
The test is set up in a highly processional working atmosphere. Everything in order. To be on the safe side, Jörg checks every screw connection, every detail, and meticulously measures all distances between the dummy and cockpit. “You always get a bit nervous”, he admits, “because you only get one attempt.” Everything is documented, and the data sheets are full of a vast number of figures.
Independent control body: the TÜV.
Oguz Meric eagerly follows the process. He's confident, because “we've already calculated all of this”, but notes that TÜV Rheinland, as a verification authority, requires a real test for certification. “It's a lot of work”, adds Peter Schmutz. And he's not just talking about the test itself. The torso was built at the Hoşdere plant near Istanbul. It was transported by truck over around 2,500 kilometres to the test centre... only to be destroyed for the pendulum impact test!
Passed with flying colours.
With bated breath, the test and development professionals go up the torso. Peter Schmutz opens the entrance door, which remained closed during an impact – also a certification criterion. Oguz Meric’s first impression: “It's looking good.” Jörg Dünschmann agrees: “I think it's passed.” Shattered glass from the windscreen covers the floor on the inside. Under the supervision of the TÜV engineer, Jörg once again measures all distances between the dummy and the cockpit.
Bartholomäus Zak from TÜV makes an initial summary: “It's looking very good; all requirements have been met.” A sheet of paper is used to check whether there is contact between the dummy and the interior. "If just one sheet of paper can fit between the dummy and the interior, that's enough", he explains. "But here, there’s definitely room for 50 sheets in-between." With the pendulum impact test a roaring success, for Peter Schmutz, one thing is certain: “Drivers of the new Setra MultiClass 500 can feel very good about working with this vehicle.”
Survival space in the MultiClass 500 LE.
The test, which is carried out with the aim of increasing driver protection, was implemented with two different torsos. Both times, the result was a positive one. These torsos were specifically selected for the most critical configurations. In the case of all variants of the MultiClass 500 LE, this means that there is sufficient survival space for the driver.