A Setra is a very special bus. This is because every Setra is the result of particularly high expectations in terms of design, comfort, safety and innovation. To this day, every Setra embodies the vision and passion of the pioneer Otto Kässbohrer to build the most modern buses of the day. One thing always remains of the utmost importance for us: the ultimate experience for drivers and passengers.
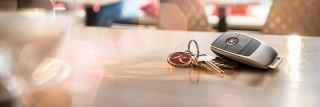
Setra World
The Setra brand
The Sign of Excellence.
Fascination Setra.
Perfection, aesthetics, passion.
The pursuit of perfection, the love of aesthetics and our passion for the extraordinary make every Setra a bus that meets the highest expectations.
Form follows function.
And man follows feeling.
Our designers have a very clear idea of what Setra design is all about. It should be unmistakable, state-of-the art and yet timeless in its own special way. But one thing is particularly important to them: each and every Setra should tell its own story through its design – and at the same time the history of our brand. A balancing act? Sure. Impossible? No way.
Our designers realise that a bus is not just a car. It is a piece of architecture and the interior is space in motion. They also know that the design must reach very different people: operators, drivers, passengers. Before they draw the first line, they therefore engage in dialogue: who are the passengers of today and tomorrow? How are their demands on travel changing? Only then do the first and initially wide range of designs emerge. With digital models and VR glasses, the designs can be experienced sensually from any angle. Gradually, a common favourite emerges in the dialogue between the decision-makers. The result is the final design for the exterior and interior of the new bus.
“A bus is space in motion, a piece of architecture.”
A Setra always remains a Setra.
Even with a custom design.
Even when it comes to design, the most important person at Setra always remains the customer. In the Setra Design Center, our consultants fulfil the customer’s individual equipment wishes. Each of them, no matter how unusual, is met with open ears here. This offers the bus operator a range of equipment with countless, individually selectable details. With modern 3D simulation programs, the customer can view the new vehicle in detail and try out variants in a manner not found anywhere else. Using a monitor, the customer goes on a “virtual walk” through the bus long before actually stepping on board for the first time. And despite all the customisation, the end result is always a genuine Setra where items complement one another. A bus that stands for excellence.
1,260 metres of experience and efficiency.
Handcrafted manufacturing with an efficient industrial process: that sounds contradictory at first, but in our assembly plant the two form a harmonious whole. Because they adhere to the same high standard: to produce unique individual buses in best Setra quality. At a full 1,260 metres, the length of our assembly line.
Not only in design, but also in assembly, less is sometimes more. This is why only one single assembly line in an orderly zigzag runs through our factory hall, on which a wide variety of bus models are produced. This has decisive advantages. Our employees save time, distance and manual actions. Above all, however, we prove with every finished bus that a high degree of customisation, efficiency, adherence to delivery dates and quality can be perfectly combined on a single assembly line.
Behind this is a sophisticated timetable: on its first “journey”, a Setra stops at about 50 stations, spending 45 minutes at each one. Enough time for a team, for example, to assemble the complete drive train, the electrical system or the heating and air-conditioning technology, to insert the panes or to lay the floor.
“At each individual assembly station we check the quality of the execution according to strict criteria.”
Even assembling the cockpit or screwing down the seats in the interior does not take more than three quarters of an hour for the team in question. Everything here is handmade by well-trained employees – and embedded in clearly defined processes. Manufactory meets industry, experience meets efficiency. And because the employees are constantly expanding their skill sets, everyone is also welcome at other assembly stations. This not only makes assembly more flexible, but also makes the job more varied. It increases motivation and has a positive effect on the quality and error rate. Which, in turn, will delight our customers in the end. Because they expect their vehicle to be of first-class quality on the promised date.
But it is not only the process that defines the quality. The high sense of responsibility of our employees also contributes to this. In addition, the quality of the work is checked and documented at each station. Futhermore, there are quality gates after certain assembly line sections. If topics need to be clarified in between, a quality coordinator is available for each station.
After six and a half days, it’s time: the new Setra is ready – and the employees proud. Specialists put the technical systems into operation. Engine, air conditioning and the entire electrical system are then fully functional. Completely cleaned, the new Setra leaves the assembly hall and starts the last stage of its first journey.
Things our robots will never learn.
In Neu-Ulm we can paint buses in over 4,500 different colours. That sounds impressive – but there is something else that is unique worldwide: we are the only company that paints buses fully automatically using robots. This has a lot of advantages – in terms of quality, environmental protection, efficiency. But there are areas where we rely solely on the skills of our employees. Areas in which robots will never attain the excellence to which we lay claim.
It’s a spectacle of a special kind. A perfect industrial choreography staged by our paint robots around the bodyshells. And it is unique in the world of buses: at 13 stations, the robots paint up to 34 vehicles every day. They draw their paths evenly and accurately, programmed and monitored by painters with the highest quality standards.
In the past, our employees used to apply the layers of paint by hand. Compared to then, today’s robots are content with about half the original amount of paint. This reduces the weight of the vehicle and protects the environment at the same time.
“No robot in the world can replace the intuition of an airbrusher or type painter.”
Everything in the paint shop follows a perfectly rehearsed procedure. Once the new body has been thoroughly washed and dried, specialists apply the yellow primer filler. The next step is one of the most important: sanding. And because the subsequent paint quality is only as good as the result of this preparatory work, our employees do not leave the sanding out of their hands.
Only now do robots make their big entrance. Layer by layer, they apply the paint to the body. And although they have great confidence in the robots, our specialists monitor the work of the robots very closely. After every single layer. Once they are satisfied with the result, the paint is dried in the drying chamber.
As perfect as our robots may be: they are not creative. That is why we have experienced professionals for specialist design tasks. Type painters, who can hardly be outdone then it comes to foil stickers. And airbrush painters who also apply filigree designs to the bus with passion and great attention to detail. No job is too difficult for them, no motive impossible. And each of them has a talent that no robot in the world can replace. They are the ones who make our buses unmistakably unique. Handcraft thus meets high tech, resulting in a very special level of quality.
Our morning round circle on the subject of better sitting.
We set things in motion for the quality of our bus seats. Take, for example, the assembly carousel of our seat factory. While it rotates imperceptibly, it always brings our seat fitters to the right place at the right time. Where the material required at that moment is waiting. This is particularly ergonomic because the components come extremely close to our employees. At the same time, the sophisticated system saves time and effort. And it contributes a lot to ensuring that the quality of our seats remains as high as it is.
How comfortable passengers feel on a bus trip depends primarily on the comfort of the seats. And we take care of this every day with great passion. Passengers expect the ultimate in comfort and relaxation, especially in a Setra. Our standards are at least as high as these expectations. Because any journey’s first destination should be the time spent in a Setra.
“Travelling well means sitting well. And we are happy to take care of that personally.”
That is why we have been manufacturing our passenger seats ourselves for over 60 years. We are the only bus manufacturer in Germany to do so. This ranges from the design, fabric cutting, sewing and upholstery to assembly. Our employees know the secrets of the best ergonomics and how perfect upholstery is made. At our carousel everyone can control the high variability of the Setra seats and can fully assemble a double seat.
Our customers can adapt the seats to their individual wishes down to the last detail. This applies to the design of the textiles as well as to all the other furnishing details. A wide range of upholstery materials is available ex works. On request, we can also produce embossing and quilting seams or embroider a logo.
Setra seats should not only be comfortable and individual, but also last a whole bus life. That is why we have developed our own very strict quality criteria. Each new fabric has to pass 25 hard tests. Only then is it allowed into our collection. And because a seat is also a central safety element, we also carry out load tests on armrests, handles and backrests. All this benefits our customers and their passengers. On every trip and for many years.
Three times to the moon.
Maybe it’s not important to take a bus three times to the moon. But it’s good to know that you could. That is why our engines are designed for a mileage of up to 1.2 million kilometres. In our opinion: if you want to build the best buses, you have to give them the best drive technology there is. And that’s called Mercedes-Benz.
When we develop a new bus, we have one thing in mind: our customers and their business. After all, Setra buses are intended to help companies look good in the face of tough competition. This has a lot to do with efficiency and sustainability. Fuel is becoming ever more precious and environmental protection ever more important. Therefore, it is our goal that every Setra should make a bus company more sustainable in the long run.
“Our goal is to make engines cleaner and more efficient at the same time.”
The engines in our buses play a key role in this. They are produced at the Mercedes-Benz engine plant in Mannheim, where many technical innovations have already gone into series production. Including the BlueEfficiency Power engines. In the further development of these components, the engineers succeeded in doing something that previously hardly seemed possible. They are cleaner than their predecessors, but at the same time more powerful, lighter and – thanks to highly efficient combustion – more economical. This not only increases the overall economic efficiency of our buses and coaches. They also prove that environmental protection, economic efficiency and performance can be successfully combined.
But long before we install one of these engines in a Setra, it has to deliver top performance from the word go. Every single one. In Mannheim, each and every engine is put through its paces on a high-tech test bench. Fully automatically and down to the last detail. After all, it is designed to keep a Setra moving reliably throughout its bus life.
In a Setra one item always fits with another when it comes to drive technology. We make an optimal engine pre-selection for each model according to its designated purpose. And we include a gearbox that interacts best with the engine. These gearboxes are manufactured with high precision in accordance with strict quality guidelines and are absolutely on a par with our engines in terms of their service life. Together with our engines they form dream couples for a long bus life. Even for three joint trips to the moon.