At the Neu-Ulm plant, Tobias Brischar is responsible for the assembly and completion of the buses and coaches. With the production changeover from three lines to one, he and his 800 colleagues have taken a big step towards even more quality and adherence to schedules.
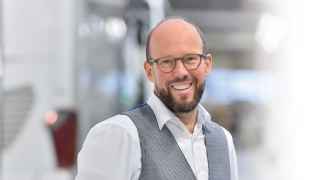
SetraWorld Magazine
Our aim is the best quality
Tobias Brischar, head of Assembly in Neu-Ulm
Our aim is the best quality.
Tobias Brischar, head of Assembly in Neu-Ulm.
Head of Assembly” says the sign on the door, yet Tobias Brischar would not describe himself as an authoritarian boss. “My job is more that of a trainer: to set out the right topics at the right time and in doing so to purposefully make use of the players’ ideas and abilities.” Especially when you want to get something moving in production, team work is particularly important, stresses the 48-year-old Swabian. “Because in a team you are much smarter than on your own.”
Tobias Brischar and his team have already got quite a lot moving. Over the last three years, the Neu-Ulm outfit has completely turned the bus and coach production upside down. In the beginning, three assembly lines worked in parallel, whilst today a single assembly line runs through the factory hall in an organised zigzag. Where assembly groups used to work sorted by trades, the employees now go about those tasks in 45 individual stations, where they are ideally completed in a 45-minute cycle. That saves time and effort and helps to prevent unnecessary manual actions.
“Because in a team you are much smarter than on your own.”
The change in the production can be clearly seen at another place too. Instead of glazed foremen offices, there is now an open terminal, where the foremen can be approached by the assembly workers at any time when problems arise. “At any one time, we construct around 100 buses here. Every day, numerous smaller and bigger issues need to be clarified, from individual special customer requests to an incorrect screw,” explains Brischar. “Workers used to go looking for a missing part themselves. Today we analyse the cause in the team and stop the problem at source.”
“Neu-Ulm is one of the most innovative factories in the EvoBus production network.”
Additional changes to quality control and error analysis are expected to provide a further improvement during the course of this year. “We want to bring about a cultural rethinking,” says Brischar. “The approach is to talk about faults and solve them instead of covering them up.” The head of Assembly expects to track down faults even more quickly by this means and to prevent subsequent and serial faults.
The “reorganisation of assembly” project is expected to be completed by the end of 2018. Tobias Brischar says the three most important aims of the changeover are better timeliness, higher quality and more efficiency. “We must always keep an eye on the customer, who expects their vehicle in first-class quality on the promised date.” With visible pleasure he tells of the project’s first successes: “Since September 2017 we have been working in the Neu-Ulm assembly without delays.”
“The production changeover at the Neu-Ulm plant was definitely the biggest challenge for me in recent years,” Brischar admits. His education as a certified pedagogue was no doubt an advantage in this respect. “Such a project requires a lot of communication, a lot of motivation and the ability to reach out to people. And last but not least the commitment of all those involved.” In other words, a bit of overtime here and there. Nevertheless, the family man, keen jogger and hobby musician still finds time for rehearsals and performances with his acoustic cover band. In this respect Tobias Brischar is also in his element when it comes to organising his free time. After all, when making music, it comes down to a well-working and coordinated team.