This year’s winter testing involved eleven vehicles from Daimler Buses, including city buses, intercity buses and touring coaches. The test was carried out over a period of more than four calendar weeks in Lapland, Finland’s northernmost region, and included a team of 36 experts altogether. Each vehicle covered between 7,500 km and 8,500 km. In a short interview, technician Bernd Gutmann explains how to prepare for winter testing and what to look out for.
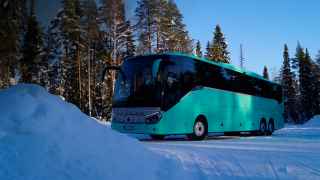
SetraWorld Magazine
Winter testing 2022 in Finland.
Interview with Bernd Gutmann, technician in the Engines, Peripherals and Chassis Test team.
Winter testing 2022 in Finland.
Tests are carried out in extreme conditions during winter testing. The vehicle and the technology must prove themselves at the lowest temperatures, on demanding routes and under adverse friction conditions (μ-low).
Mr Gutmann, winter testing is an important milestone for our vehicles. What do you need to bear in mind at the beginning when preparing for winter testing?
We start preparing and planning six months in advance. At the beginning, the topics and corresponding time requirements are obtained from the individual specialist teams. The as-built configurations are then coordinated step-by-step with the Design department and our suppliers. At the same time, we start organising the trip behind the scenes. This includes, for example, booking the hotels, selecting the routes and obtaining approvals in line with national regulations. Covid-19 also meant that the pandemic regulations of the individual countries had to be taken into account. Shortly before leaving for Finland, things usually get hectic as the last late components and software versions are “traditionally” delivered just before departure.
What actually happens during winter testing?
The vehicles start in Germany and drive towards the Arctic Circle to Rovaniemi in Finland via Denmark and Sweden. A team consisting of an engineer or technician and mechatronics engineer is assigned to each vehicle. The journey takes four days both ways. We cover almost 3,000 km in each direction. Even the time it takes to reach the far north is used for initial measurements.
What exactly is checked during winter testing?
The main technical drivers for winter testing are primarily cold-weather testing of the various systems and the suitability of the vehicles for low friction in winter conditions. All vehicle systems, for example, chassis, engine and transmission, behave differently in very cold temperatures of down to -35°C than under typical central European conditions between 10 and 20°C. Rubber mounts, shock absorbers, but also all fluids, such as oils, demonstrate changed properties in very cold conditions and can therefore have a significant influence on the vehicle's behaviour (for example, driving, shifting and starting behaviours). The elements we analyse onsite are very diverse - from functional tests of the systems, components and software versions to dynamic driving manoeuvres and active fault simulation.
Why is testing carried out in Finland?
We utilise the facilities and test track located at the Arctic Circle in Rovaniemi, the capital of Lapland along with our colleagues from Trucks and Special-purpose Vehicles (Unimog and Econic). In addition to the economic advantage of the shared use of the facilities, the various organisational units also compare their experiences in terms of the technology.
What was special about this year’s winter testing?
In 2022, we paid particular attention to the issue of travelling under pandemic conditions. This year, for example, we largely avoided using ferries and flights to reduce the risk of infection as much as possible when travelling to and fro. As a result, the day stages and stop-off points were reorganised. As a key component in the overall hygiene concept for winter testing, all of our buses were equipped with active filters with anti-viral functional layers for the interior. Other hygiene measures, such as disinfectant dispensers, masks and workstations with social distancing were also implemented in all buses and touring coaches. In order to keep the risk of infection low during testing, a sufficient number of masks and rapid tests were provided by the company. Each participant also voluntarily committed to keeping social contact outside of the group to a minimum.
At this year’s winter testing, ComfortClass and TopClass facelift vehicles, which will premiere in the autumn, already underwent as well. Can you tell us here what was tested in the vehicles?
Some elements and components that are incorporated in the Setra facelift of the ComfortClass and TopClass have been in development for some time and have already been subjected to several tests: from initial, preliminary investigations to various maturity levels and software versions to series production release. The first tests were integrated in existing and rather inconspicuous vehicles. Entire vehicles were assembled and maturity levels increased as we approached the production launch. They then had to prove their capabilities as an overall package. Vehicles were of course camouflaged during this year’s winter testing. Elements such as the driveline with engine and transmission, brake systems with EBS and ESC, the assistance systems and the overall vehicle with exterior attachments were also incuded this year.