Pronti al confronto: il telaio a sezione frontale del nuovo Setra MultiClass 500 LE e un intero arsenale di minacciosi cilindri idraulici. Il conto alla rovescia è breve, quindi la pressione è ancora maggiore: «Tre, due, uno, via!», conta Peter Schmutz. Un cilindro idraulico pressa una lastra d'acciaio di 250 x 400 mm sulla nuova protezione antincastro Setra MultiClass 500 LE in cinque punti definiti, uno dopo l'altro, con una pressione di otto o 16 tonnellate.
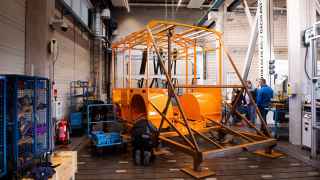
SetraWorld Rivista
Sicurezza passiva migliorata.
La nuova MultiClass 500 LE dispone di una protezione antincastro anteriore.
Sicurezza passiva migliorata.
La nuova MultiClass 500 LE dispone di una protezione antincastro anteriore.
«Il marchio Setra è sinonimo di sicurezza. Ecco perché i nostri autobus sono progettati di conseguenza. Con questi test dimostriamo che i nostri prodotti soddisfano i requisiti stabiliti.»
Peter Schmutz lavora nel settore test di Daimler Buses ed è responsabile dei test sulla sicurezza passiva da oltre dieci anni. Grazie alla sua vasta esperienza, ha una profonda conoscenza di ciò che sta facendo. «Il marchio Setra è sinonimo di sicurezza. Per questo motivo progettiamo i nostri autobus e pullman tenendo conto di questo aspetto. Test come questo dimostrano che i nostri prodotti soddisfano i requisiti stabiliti".
«Nel caso di un impatto frontale con un'autovettura, si deve impedire che quest'ultima «si incastri».»
Test volontario.
A differenza degli autocarri, per gli autobus la protezione antincastro non è prescritta per legge. L'equipaggiamento a richiesta protezione antincastro della nuova MultiClass 500 LE è costituito da una traversa e da rinforzi retrostanti. La struttura serve principalmente alla protezione dei partner. «In caso di impatto frontale di un'autovettura si deve impedire che scenda sotto di essa», spiega Deniz Uçur, sviluppatore della scocca presso Daimler Buses.
Se Daimler Buses sta testando, allora è giusto. Pertanto viene eseguito il collaudo secondo il Regolamento UN/ECE 93. Essa indica da un lato le dimensioni e la posizione della protezione antincastro e dall'altro la posizione dei punti di applicazione del carico, le forze di prova e la massima deformazione ammessa.
Simulazione di incidenti.
Teatro dell'perazione è l'edificio 200, il capannone del banco di prova nel Centro di sviluppo e collaudo (EVZ) di Daimler Truck a Wörth am Rhein. Qui non vengono testati solo gli autocarri, ma occasionalmente anche gli autobus per quanto riguarda la loro sicurezza passiva. Tutti i test simulano incidenti. Essi servono quindi alla sicurezza del conducente, dei passeggeri e degli altri utenti della strada coinvolti in un incidente.
Almeno un test alla settimana.
Jörg Dünschmann, ingegnere collaudatore di Daimler Truck, è responsabile del capannone del banco di prova. Con l'aiuto di una gru, lui e il suo team portano l'ossatura dell'autobus nelle cinque diverse posizioni di prova. In ogni posizione viene avvitato saldamente in quattro punti sul pavimento del capannone e inoltre ancorato con catene - infine deve resistere a un carico di pressione enorme.
Condizioni di prova ideali.
Le telecamere catturano ogni momento del controllo. Nella sala di controllo, il team di prova segue l'esperimento, osservando ciò che accade attraverso finestre e schermi. Qui ha preso posto anche Bartholomäus Zak del TÜV Rheinland. L'ingegnere addetto alle prove di omologazione controlla il processo e i risultati dei test e rilascia infine la certificazione richiesta. Perché è chiaro: la sicurezza costruita è buona, la sicurezza testata è migliore, la sicurezza certificata è impareggiabile. Considerati i risultati ottenuti, Peter Schmutz è sicuro: «Siamo un punto di riferimento per la sicurezza passiva.» Buono a sapersi.